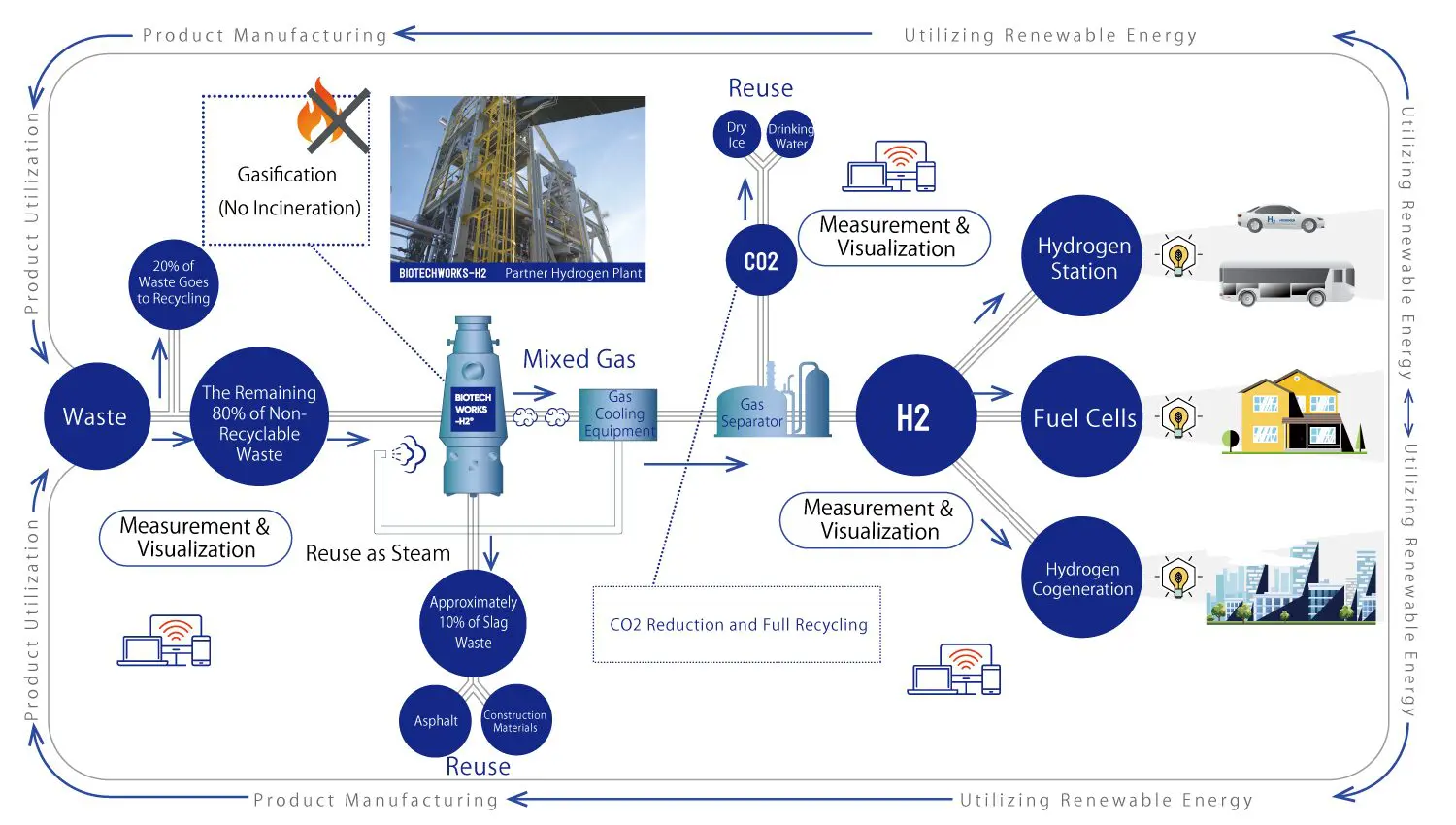
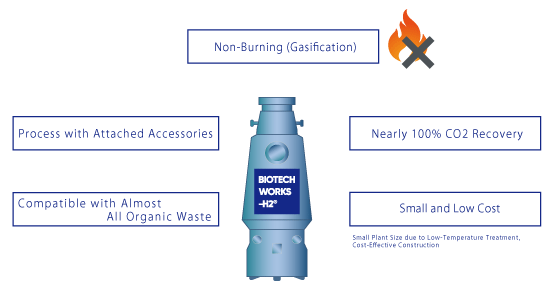
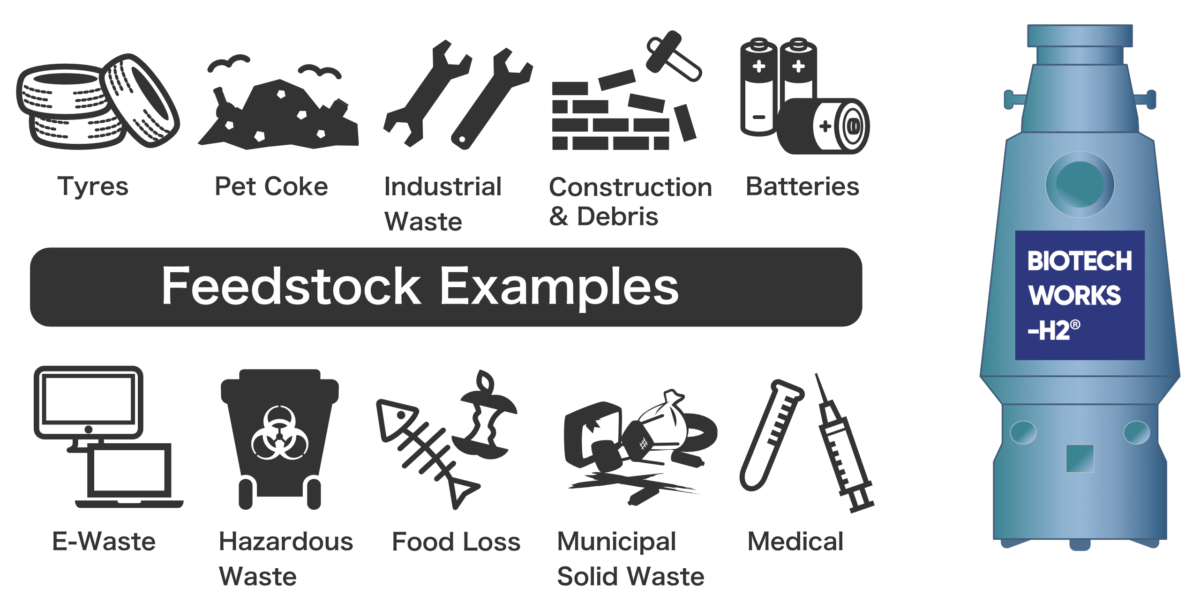
①Preparation
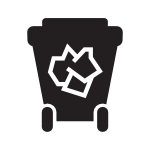
Our gasification converts a wide array of waste into energy through non-combustion methods.
②Process
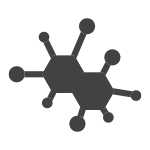
Our gasifier uses heat, steam and oxygen to break down waste at the molecular level.
③Conversion
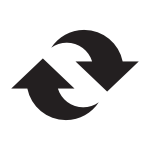
Organic materials in the waste melt and reform into energy-dense syngas.
Inorganic materials in the waste melt and are recovered as a non-leaching inert stone and metals.
④Final Product
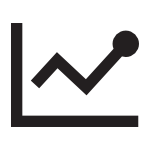
Waste turns into tar-free syngas suitable for conversion to the required end-product.
⑤By-product
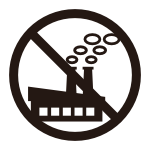
There are no ash or other toxic byproducts that require further disposal.
Benefits
Condensable tars in the raw syngas exiting the top of the bed are fully converted to additional syngas using controlled reactions with oxygen and stream at 2,000°F(1,100℃).
The tar-free syngas then exits the top of the gasifier ready for downstream processing.
Oxygen and steam are injected into the bottom of the gasifier producing hot syngas that rises and exchanges heat with the bed of waste material.
This supports additional gasification reactions, devolatilization, and drying.
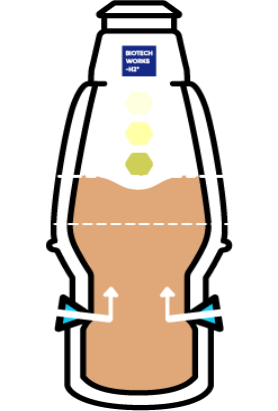
Waste enters the side of gasifier and is dried by rising hot syngas. The waste then descends into the devolatilization zone where a mix of light gases, hydrocarbons, and condensable tars are released at 1,300°F(704℃).
Solids that escape with the gas are cleaned out of the syngas and recycled back into the gasifier during gas cleaning.
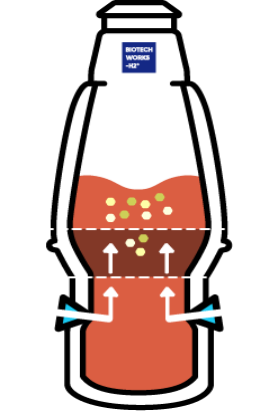
Gasification occurs in the lower section of the vessel where the remaining carbon-containing materials in the waste react with the steam and oxygen.
The exothermic gasification reaction raises the temperature of the lower zone from about 2,500°F(1,371℃) to 4,000°F(2,204℃) allowing for the through conversation of remaining carbon into syngas; the large amount of energy produced at this stage allows the system to be self-sustaining.
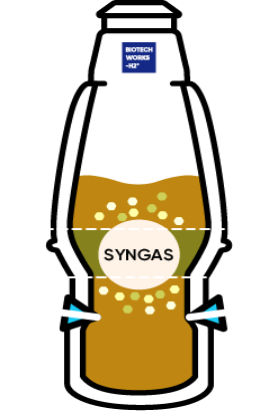
At 4,000°F(2,204℃), inorganic compounds and metals melt and collect at the bottom in a molten state. This is removed as non-leaching inert stone and recovered metals.
The ultra temperatures of the gasification allow the system to completely convert mixed waste without producing toxic by-products.
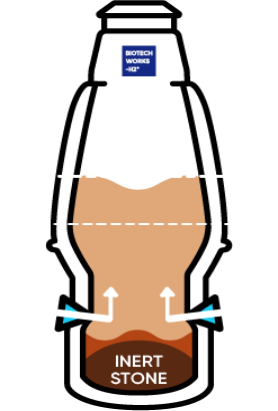